Stedman Machine Cage Mills
Stedman’s range of multi-cage mills and pulverizers includes the H-Series, F-Series for sticky, high moisture and Y-Series designed for less abrasive material applications. In general, the larger the pulverizer, the larger the feed size it will accept and the greater capacity it will produce. Capacity also depends on upon the speed at which the mill is operated, the feed size and its specific gravity, and the size of the desired product. Cage mills work by reducing the material they are fed to predetermined smaller sizes by striking repeatedly with cage pins and throwing the particles at high speed against each other, against the cage mill housing and against the other pins.
Industrial Pulverizing Equipment Features & Benefits
- Up to 40:1 Reduction Ratio
- 2 to 7 Hp per ton
- Tertiary crusher–for fine material
- Wet & sticky material is NOT a problem
What is a Single Row Cage Mill?
Single-row mills, although normally classified as secondary crushers, are designed for heavy-duty crushing, frequently of hard and highly abrasive materials, although their versatility makes them valuable for the reduction of many kinds of materials. They are particularly useful in the beneficiation of sand and gravel and in the upgrading and crushing of all kinds of aggregates, ores and coal.
What is a Multi-Row Cage Mill?
Multi-row mills normally consist of an even number of cages: two, four or six. The cages are arranged concentrically, with each cage spinning in the opposite direction from that of the cage adjacent to it. A multi-row cage mill employs multiple stages of selective impact reduction. The material to be reduced is fed into the center of the innermost cage, where it is struck by the massive spinning pins and distributed 360 degrees around the cage. Centrifugal force and the impact of the pins causes the material, now reduced to smaller pieces, to pass through the cage into the pins of the next cage, which is spinning in the opposite direction. The farther away from the center cage the particles travel, the more their impact velocity is increased.
Test Before You Buy™
The Stedman Testing and Toll Processing Facility is the place to test your material in our full size equipment. If it can be crushed, ground, pulverized or mixed, chances are we’ve done it. We have more than 10,000 test reports to help get you to the best solution quickly. To learn more about what to expect from testing, read our article that ran in POWDER BULK ENGINEERING magazine.
Industries
Stedman Machine Company’s line of size-reduction equipment is found in industries and applications from A-to-Z. In fact, it would be easier to list the industries that don’t employ some type of size-reduction equipment!
Rock & Aggregate Crushers
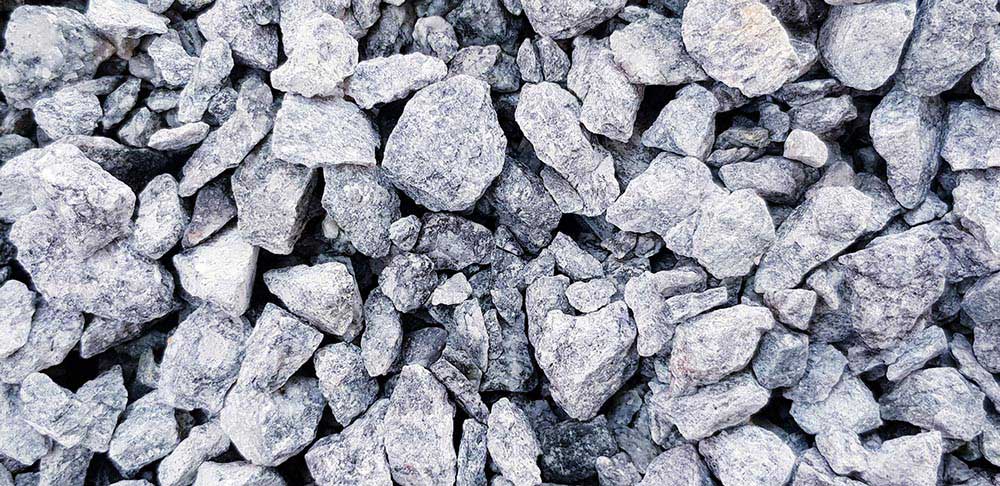
Specialty uses of limestone include the manufacturing of pharmaceuticals, toothpaste, paint, paper, caulking, and glass.
Energy & Biomass Pulverizers
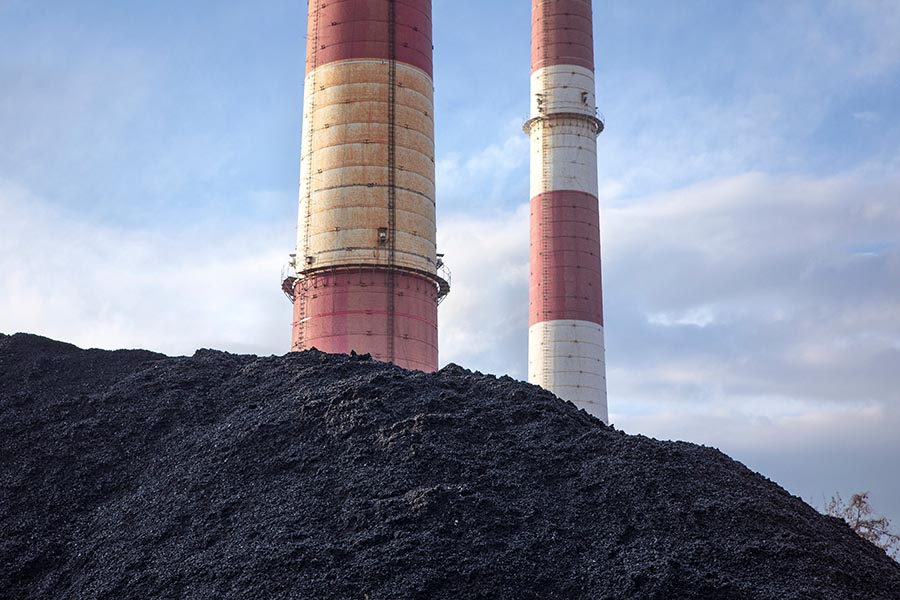
One of the first uses for the cage mill was as a coal pulverizer. By 1900 Nathan Stedman had built more than 100 cage mills designed to crush coal.
Ceramic & Brick Clay Crushers
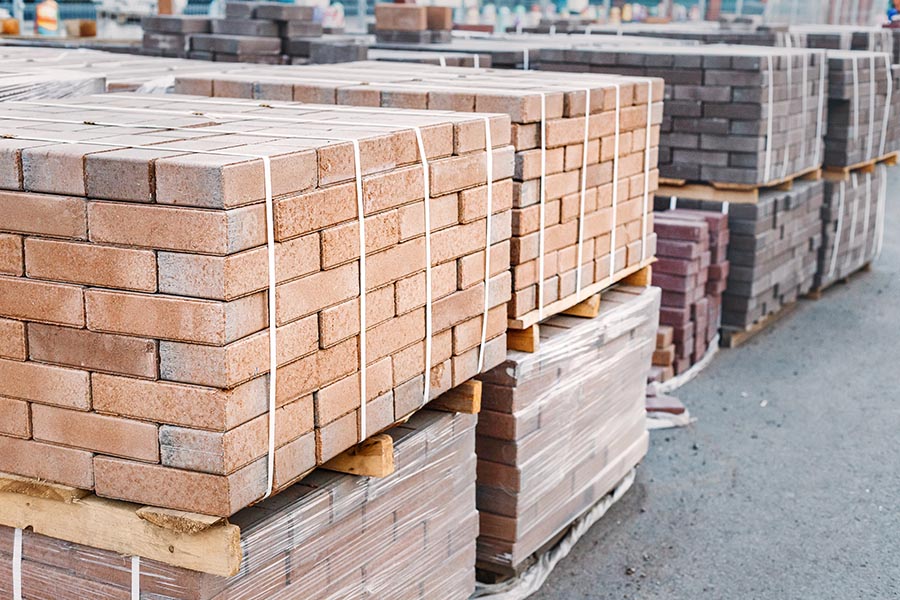
Stedman revolutionized material preparation for the brick, clay, and ceramic industries by introducing more cost-efficient processes.
Size reduction for a variety of minerals
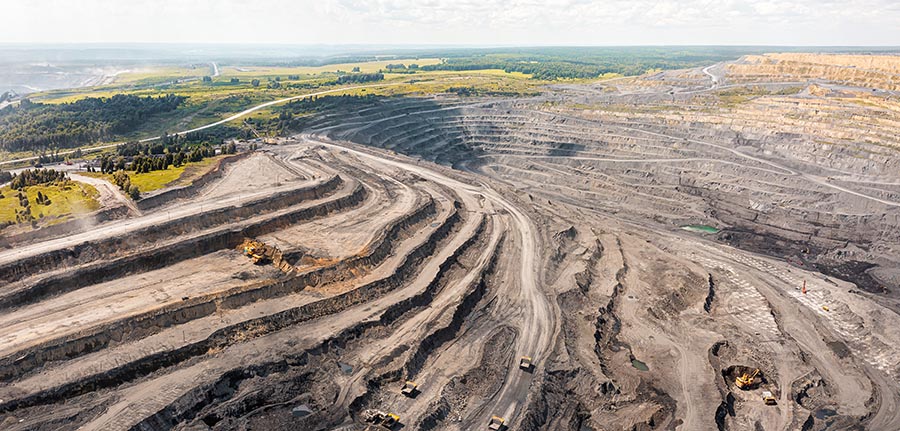
Stedman crushers, mills, and grinders are used in nearly every mineral and mining industry. Whether you are processing coal, rock, salt, iron ore, wood chips or clay, we have your solution to size reduction.
Industrial Food Rendering Crushers
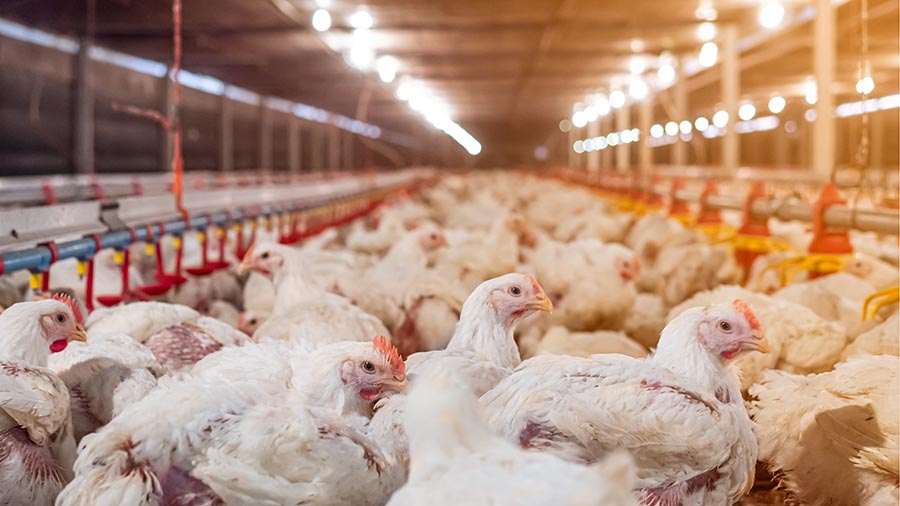
Stedman ensures nothing goes to waste by delivering reliable, durable pulverizers and crushers perfect for handling food waste and food rendering.
Agricultural Crushers

Stedman delivers high-performing pulverizers crushers perfect for agricultural uses including crushing lime, processing animal feed, and reducing grain corn.
Industrial Herb & Spice Crushing Equipment
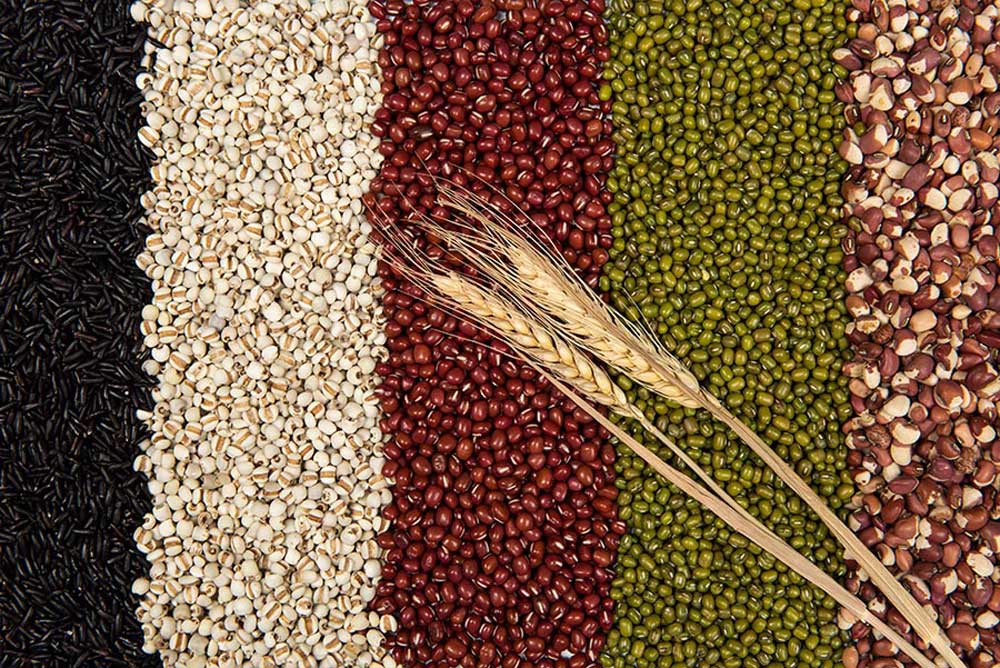
Stedman delivers high-performing, low-maintenance pulverizers crushers ideal for large-scale grinding, milling, and processing of herbs and spices.
Grain Processing Equipment for Distilleries
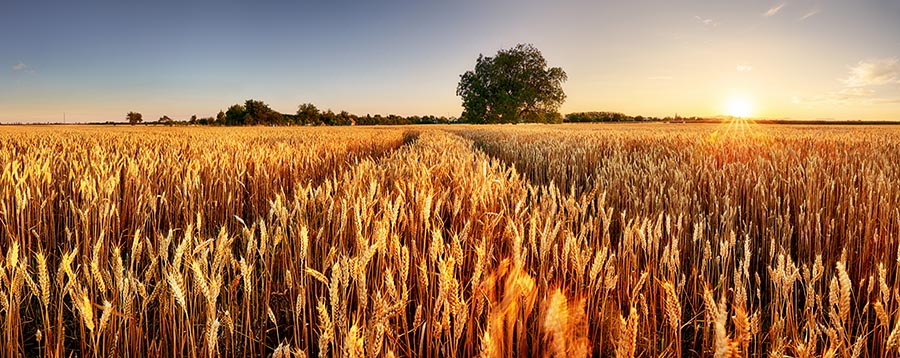
Stedman delivers high-performing, low-maintenance pulverizers & crushers ideal for large-scale grinding and milling grain and corn to supply distilleries.
Fertilizer Crushing Equipment
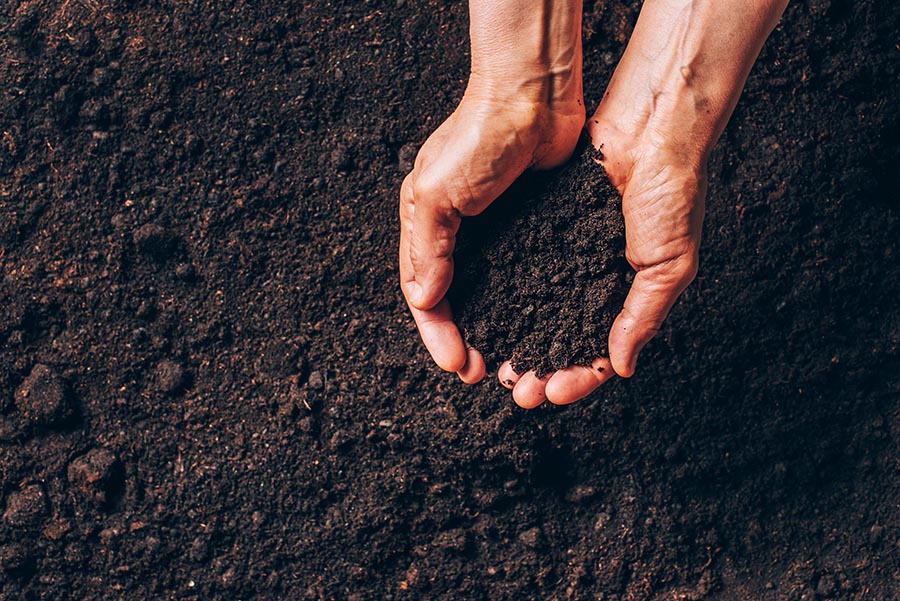
Stedman’s reliable, durable lump breakers, chain mills, and cage mills are expertly engineered, sturdily constructed, and rigidly tested to meet the specifications you require for heavy-duty fertilizer processing and size reduction.
Additional Information
Delivering equipment and service you deserve
For nearly two centuries, Stedman Machine Company has produced quality, reliable and durable size reduction and industrial crushing equipment. Stedman has expert field service and installation technicians ready to assist with all maintenance and equipment commissioning needs.
- Unsurpassed industry experience – operating since 1834
- State-of-the-art equipment testing facilities
- Dedicated, professional staff
- Parts and service available 24 hours a day
Stedman Machine is a leading cement crusher manufacturer with the capability to provide customer service across the globe. Our experienced team will work with you to create the best impact crusher system to make your processes the most efficient. Call us for more information!
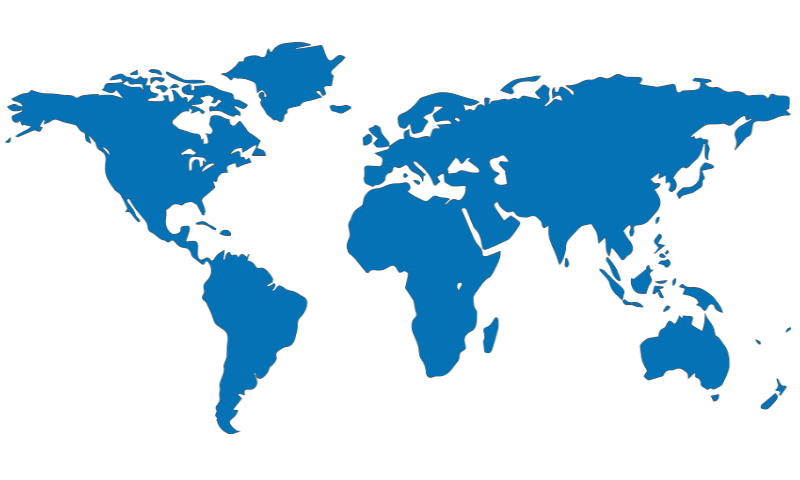
Resources
Contact Us
Our 24 hour parts and service department along with our inventory of wear parts allow us to provide the fastest response time for parts and service.